8 Critical Considerations for Choosing High-Quality Conveyor Belts
Selecting the right belt is not just about specifications - it envolves foresight, precision, and understanding the unspoken demands of your operations. Whether you are a distributor selecting products for your clients or an end-user equipping your production lines, understanding what truly defines a high-quality conveyor belt is critical. This guide walks you through the essential features that make a high quality conveyor belts: material durability, tensile strength, flexibility, surface profiles, chemical resistance, certifications, and maintenance factors — that determine long-term performance and value. Making wise choice ensures less downtime, lower Total Cost of Ownership, and increased customer and business satisfaction.
1. Material Quality: The Backbone of Longevity
A conveyor belt is only as reliable as its weakest layer. A high-quality belt uses strong cover compounds that resist abrasion, tearing, and impacts, as wear on the cover exposes the carcass to premature failure. Look for belts tested under ISO 14890/DIN 22102 abrasion classes – a lower volume loss (in mm³) means better wear resistance. The belt carcass (fabric layers or steel cords) provides strength: heavy-duty steel-cord belts have very high tensile strength and can be used for long-haul, high-load use (e.g. mining), fabric-ply-belts are lighter but rugged enough for the general material handling.
Check how many fabric plies the belt has and how they are bonded together. Better belts use strong fabric (polyester/nylon/aramid) with tight adhesion (ISO 283/ISO 6133 testing), so that layers do not delaminate when under pressure.
2. Tensile Strength and Elongation
Tensile strength and elongation tell you how much force the belt can take before it stretches or breaks.
Tensile strength is usually given in MPa or N/mm and measured per ISO 37 or ASTM D378. For example, a belt rated 20 MPa means it can withstand a pulling force of 20 MPa before failing. Belts with higher tensile ratings will handle heavier loads and longer spans without excessive stretch.
Working Load 1% Elongation refers to the load, measured in N/mm, that would cause the belt to lengthen by 1% of its original length.
Elongation at break is a percentage that indicates how much a belt can stretch under tension; while some stretch is normal, too much elongation means sag and loss of control. Belt data sheets from a qualified manufacturer specify both strength and elongation.
-
Safety margin: A premium belt often exceeds the stated spec (e.g. ≥10% over stated tensile) to avoid “blind acceptance” of bare-minimum quality.
-
Units and codes: Be aware of standard codes (e.g. ISO 14890 class, DIN grades, or PIW values). Ask the supplier for the actual tensile strength (MPa or kN/m) and elongation data, not just the class name.
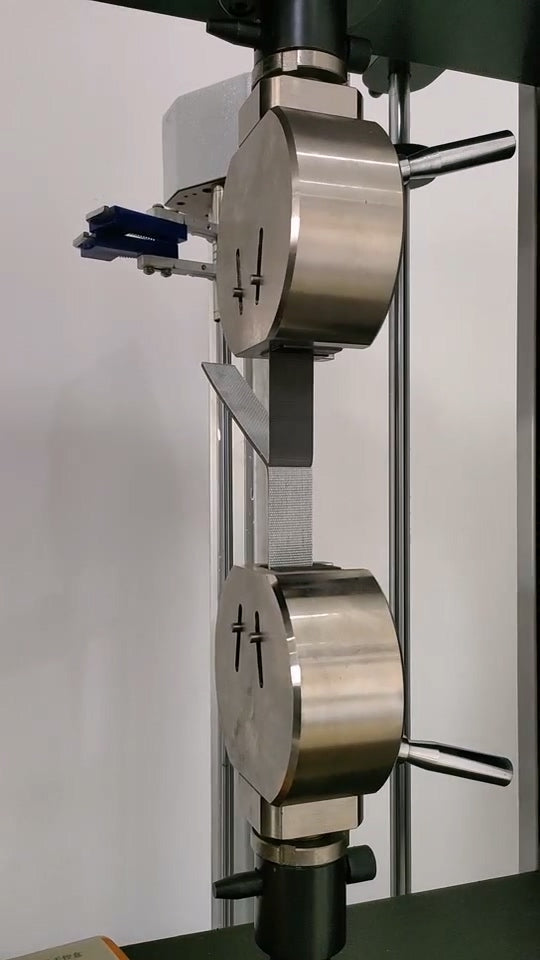
3. Flexibility and Bend Radius
Flexibility matters, especially for conveyor systems with curves, small pulleys, or tight layouts. Flexible belts can bend around small-diameter pulleys and follow curved paths without damage. Fabric-layered or polymer (PVC/PU/...) belts are usually very pliable and can easily adapt to any conveyor shape. In contrast, stiff steel-cord belts require larger pulley diameters and straight runway. Always check the manufacturer’s specified minimum pulley diameter for a given belt. In general, choose a belt whose flexibility matches your system: use a more flexible belt for compact or serpentine conveyors, and a stiffer belt where long straight runs or heavy loads dictate it.
4. Surface Profile and Traction
The top surface of the belt determines how it grips or releases material. Smooth, low-friction covers are easy to clean and ideal for delicate products, while textured or patterned surfaces improve grip for loose materials and slope conveying.
A well-established conveyor belt manufacturer always offer custom surface pattern and embossings to meet every possible industry needs – for example, the food and beverage sector demands hygienic, easy-to-clean surface to meet strict sanitation standards, while the marble processing industry needs soft contact to avoid surface scratches and anti-slip embossings to enhance grip.
Moreover, cleats/flights can be moulded on the belt for bulk materials and steep angles, sidewalls can be added if containment is needed.
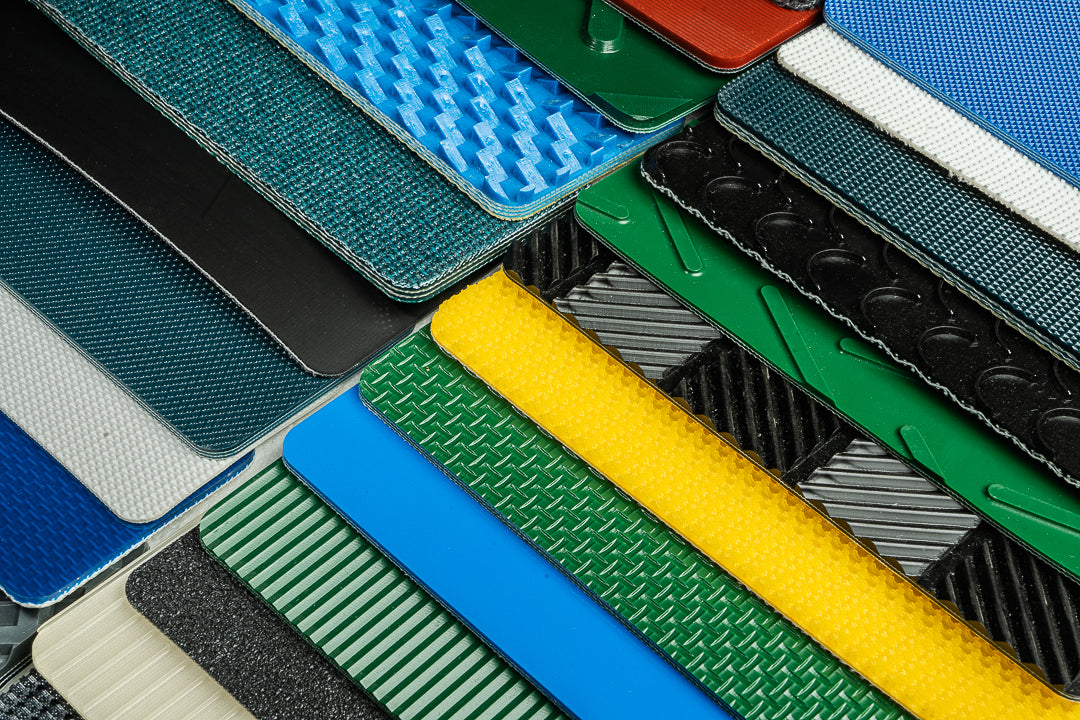
5. Chemical and Environmental Resistance
Consider the environment and materials the belt will encounter. Chemical compatibility is crucial: certain material compounds resist oils, acids, and solvents better than others. For example, Thermoplastic Polyurethane (TPU) is prized for oil- and fat-resistance (common in food or oily factories), while Neoprene (CR) rubber is durable against weathering and many chemicals. If the belt carries corrosive or acidic materials (pulp, fertilizer, salts), look for belts labeled “chemical-resistant” or “acid/alkali resistant” (often made of special EPDM or PVC compounds). Likewise, if the belt will be in very hot ovens or freezers, choose a material rated for those temperatures (silicone belts for extreme heat, PVC/PU belts remain flexible in cold).
-
Oil/Fat Resistance: Food-industry belts often use FDA-approved food-grade PVC or polyurethane belt that resists oils, fats, and cleaning agents.
-
Flame and Static: If safety regulations apply (airport belt for example), choose belts rated for flame retardance (e.g. EN 12882/ISO 340) and antistatic (ISO 284). Flame-resistant belts have covers formulated to self-extinguish, and antistatic belts prevent dangerous charge build-up.
6. Customization Options
Mature conveyor belt manufacturers like Kunming Conveyor Belt offer extensive customization to meet unique needs. You should be able to specify belt dimensions (width, length, thickness) to fit your equipment, surface profiles to meet your conveying angles and materials. Colors can denote material or aid in food sorting (e.g. blue or white food belts). Many belts can be fitted with metal-detectable strips (for food safety) or conductive threads (to dissipate static).
Add-ons like cleats, fasteners, sidewalls are often available to order. For example, you can request belts with built-in cleats or spacers every X inches, or perforated for vacuum or knife transfers.
Key takeaway: a good belt supplier will let you tailor the belt construction (materials, covers, and accessories) to your application. Always confirm these options before purchase so the belt is built to spec.
7. Certifications and Standards
Reputable belts come with proper certifications or compliance statements. For general quality assurance, a good manufacturers hold ISO 9001 (quality management) certification, which means their production processes are controlled and audited. More directly, belts themselves may be tested or certified to relevant standards:
In food and pharmaceutical industries, look for belts made to food-grade standards. In the EU, belts should comply with EC 1935/2004 and EU 10/2011 (migration limits). In the US, The FDA has compiled a list of raw materials which are permissible in the belt coatings, and the manufacturer must ensure that the belt’s raw materials are FDA-compliant for food contact. Many of KCB's food belts are made to meet both FDA and EU rules, and often to ISO 22000/HACCP food safety management principles. Some belts also carry USDA or NSF food-grade certifications for meat/dairy use.
In summary, verify that the belt meets any industry-specific standards you need (flame, food-safety, antistatic, etc.).
8. Maintenance and Longevity
A good conveyor belt should be easy to maintain, saving you downtime and repair costs. Material choice affects cleaning: smooth, homogeneous belts (e.g. monolithic PU) have no seams or crevices to trap debris or bacteria, making wash-down faster and more effective. Similarly, belts with frayless or sealed edges will not fray and can withstand scrapers and brushes. In food plants, belts designed for Clean-In-Place (CIP) processes (like positive-drive PU belts) greatly reduce cleaning time.
Routine upkeep tips: conduct regular inspections for wear or damage (look for cracks, delamination or fraying) and clean the belt often to prevent material buildup. Keep the belt properly tensioned and aligned, as mis-tracking causes uneven wear. Use the correct lubrication on bearings and rollers to avoid excess friction on the belt. If a belt section does wear out, ease of repair matters: belts that allow quick mechanical splicing or pin-lacing mean you can fix a damaged section without replacing the entire length. In short, pick belts known for long life, but plan for preventive maintenance: the right belt will minimize the frequency of repairs.
Read Maximizing Efficiency And Longevity: How To Get The Most Out Of Your Conveyor Belts? for more detailed guidance for conveyor belt maintenance.
Conclusion
Selecting the right conveyor belt is far more than just matching basic specifications — it’s about securing a durable, efficient, and reliable solution tailored to your operating environment. By focusing on key features like material strength, flexibility, surface design, environmental resistance, and compliance certifications, you not only enhance system performance but also minimize the Total Cost of Ownership. Whether you’re a reseller advising clients or an end-user optimizing your process, investing in high-quality conveyor belts will save you time, money, and headaches in the long run. Choose wisely today, and your operations will run smoother tomorrow.
Kunming Conveyor Belt is one of the most reputable conveyor belt manufacturer in the world, your trusted partner for belting solutions. Contact us anytime for expert suggestions if you have any questions about choosing conveyor belts!
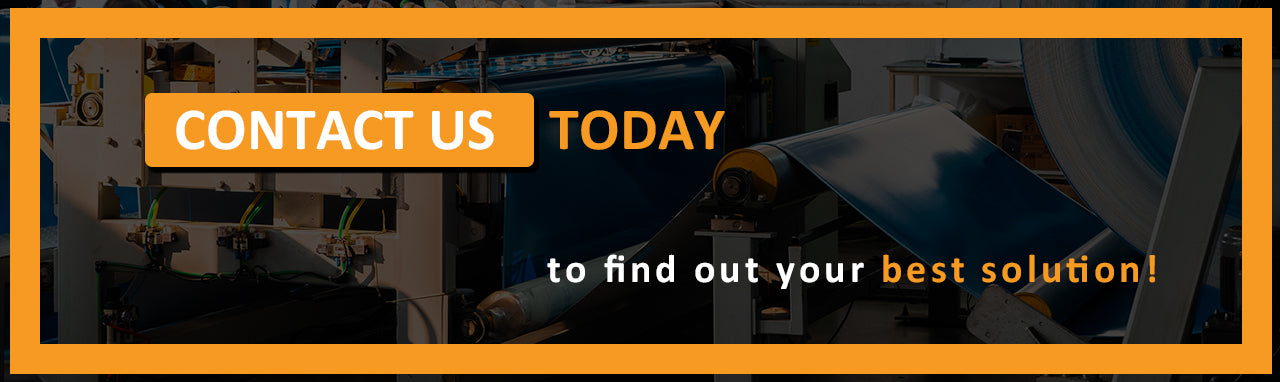